How should the water well drilling rig deal with different soil layers?
In the actual drilling process, UY water well drilling rigs often encounter various complex soil layers. These different soil layers have unique physical properties and chemical characteristics, which bring different degrees of challenges to the drilling process. In order to ensure the smooth progress of the water well drilling rig drilling process, targeted treatment measures need to be adopted according to the characteristics of each soil layer.
1.Treatment of gypsum layer
The gypsum layer is usually hard and brittle. During the drilling process of the water well drilling rig, gypsum may react with the drilling fluid, resulting in blockage of the borehole, adhesion of the drill bit and other problems. In order to effectively deal with this problem, the treatment methods include:
(1) Pretreatment of drilling fluid: Before drilling the gypsum layer, the formula of the drilling fluid needs to be specially adjusted. Increase the concentration of calcium ions to enhance the stability of the drilling fluid to gypsum. Generally, adding an appropriate amount of polymers and bentonite can help the drilling fluid better compete with the gypsum layer and reduce the chance of blockage.
(2) Adding anti-gypsum agents: Some anti-gypsum chemical agents can be used, such as soda ash, decalcifiers or organic acid additives. These chemicals can neutralize the calcium ions in gypsum, prevent gypsum crystallization, and ensure that the fluidity of the drilling fluid is not affected.
(3) Increasing the pH value: In order to improve the anti-pollution ability of the drilling fluid, the pH value of the drilling fluid can be appropriately increased, usually adjusted to between 9 and 10, to reduce the interaction between gypsum and the drilling fluid.
(4) Using rheological regulators: If the gypsum layer is relatively hard, using regulators to increase the rheology of the drilling fluid and increase the viscosity of the drilling fluid can effectively slow down the friction between the gypsum and the drill bit and avoid excessive wear of the drill bit.
Through the above measures, the pollution of the drilling fluid by gypsum can be effectively prevented, and the equipment failure rate caused by the gypsum layer during the drilling process can be reduced.
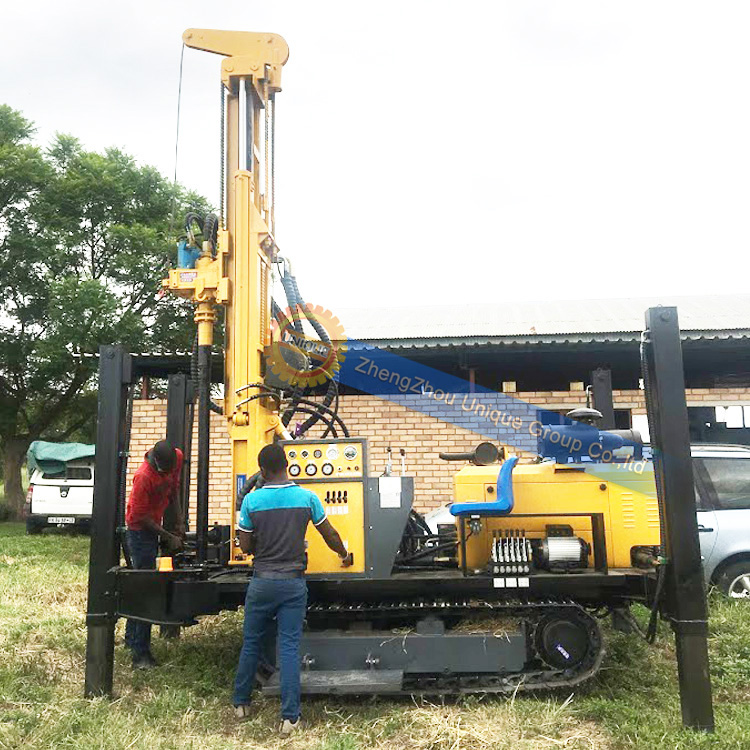
2.Treatment of quicksand layer
The quicksand layer is mainly composed of loose sand particles with large porosity and soft soil. When a water well drilling rig drills into a quicksand layer, it is easy to collapse or the sand layer enters the hole, affecting the stability of the drilling. Therefore, when dealing with quicksand layers, special attention should be paid to the following points:
(1) Increase the viscosity of the drilling fluid: In the quicksand layer, in order to ensure that the drilling fluid can effectively support the hole wall and prevent the quicksand layer from collapsing, it is necessary to increase the bentonite content in the drilling fluid to 10%-15%. Bentonite can effectively increase the viscosity of the drilling fluid, form a stronger mud cake layer, and reduce the penetration of quicksand.
(2) Add high-viscosity materials: In addition to bentonite, some high-viscosity materials, such as polymers or synthetic polymers (for example, polyvinyl alcohol), can also be used to enhance the adhesion of the drilling fluid and help stabilize the hole wall.
(3) Use sealing drilling fluid: Before drilling, you can use a drilling fluid with better sealing properties. The common practice is to use water-based mud with a viscosity requirement of more than 80cP to ensure that the quicksand layer can be effectively sealed to prevent the loosening and collapse of the borehole wall.
(4) Control the pumping volume: Since the soil in the quicksand layer is loose, excessive displacement may cause sand to fall into the hole. Therefore, the displacement of the drilling rig can be appropriately reduced to reduce the impact of the mud and avoid the invasion of quicksand.
(5) Regularly clean the borehole: Since the quicksand layer is relatively soft, the water well drilling rig needs to clean the borehole regularly during drilling to promptly remove the sand mixed in the drill bit and drilling fluid, keep the borehole unobstructed, and avoid sand accumulation affecting drilling.
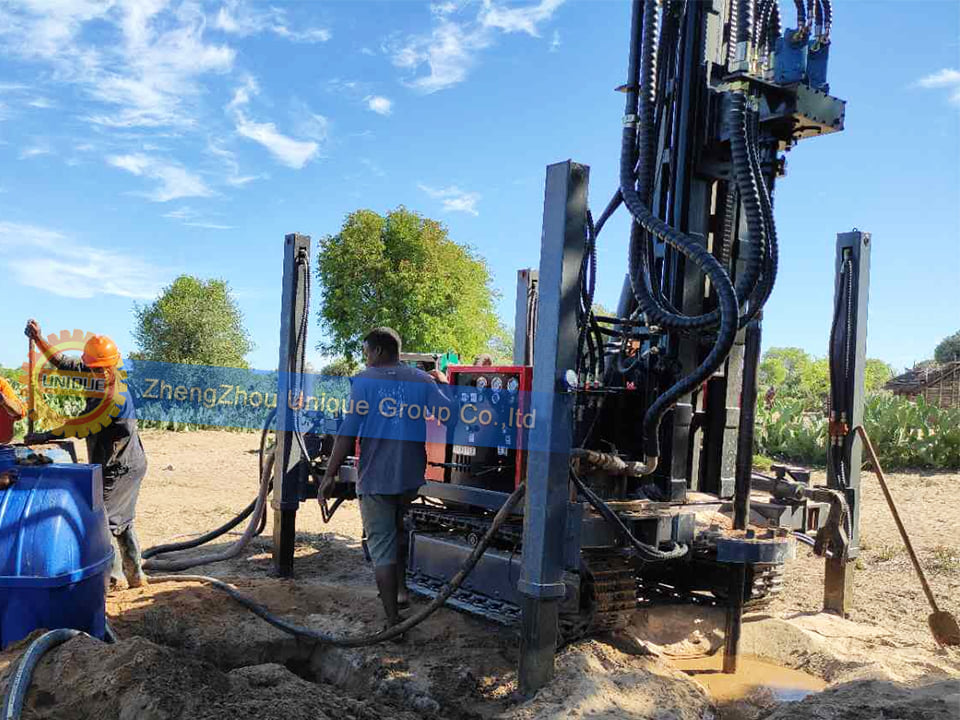
3.Treatment of quartz sandstone layer
Quartz sandstone layer is usually composed of hard quartz minerals with high hardness and brittleness. During drilling, problems such as drill bit jumping and rock debris accumulation are prone to occur. The treatment of quartz sandstone layer mainly includes the following methods:
(1) Use diamond drill bit: Since quartz sandstone has a high hardness, conventional drill bits may wear out quickly. Therefore, using diamond drill bits (such as polycrystalline diamond drill bits) is a more common choice. This type of drill bit can withstand higher drilling pressure and effectively improve drilling efficiency.
(2) Optimize drilling speed and pressure: When drilling, it is necessary to control the drilling speed to avoid damage or vibration of the drill bit due to excessive speed. Excessive drilling speed will cause high-frequency vibration of the drill bit, increase loss, and fail to clean up the cuttings efficiently. Reasonable drilling speed can effectively avoid drill bit vibration and improve stability.
(3) Add lubricant: Drilling of quartz sandstone easily leads to increased friction between the drill bit surface and the rock surface, increasing the chance of drill bit wear and vibration. To solve this problem, lubricants can be used to reduce the friction coefficient, maintain smooth contact between the drill bit and the rock formation, and reduce vibration.
(4) Remove cuttings in time: During the drilling process, quartz sandstone will produce a large amount of cuttings. If they are not removed in time, the cuttings may accumulate around the drill bit, causing drilling obstruction. The formula of the drilling fluid can be adjusted to increase its cleaning effect, ensure that the cuttings can be effectively removed from the borehole, and avoid blockage.
(5) Use drilling tools with hydraulic cutting function: Hydraulic cutting drilling tools can adjust the drill bit pressure through the hydraulic system, thereby improving cutting efficiency and reducing damage to the drill bit during drilling.
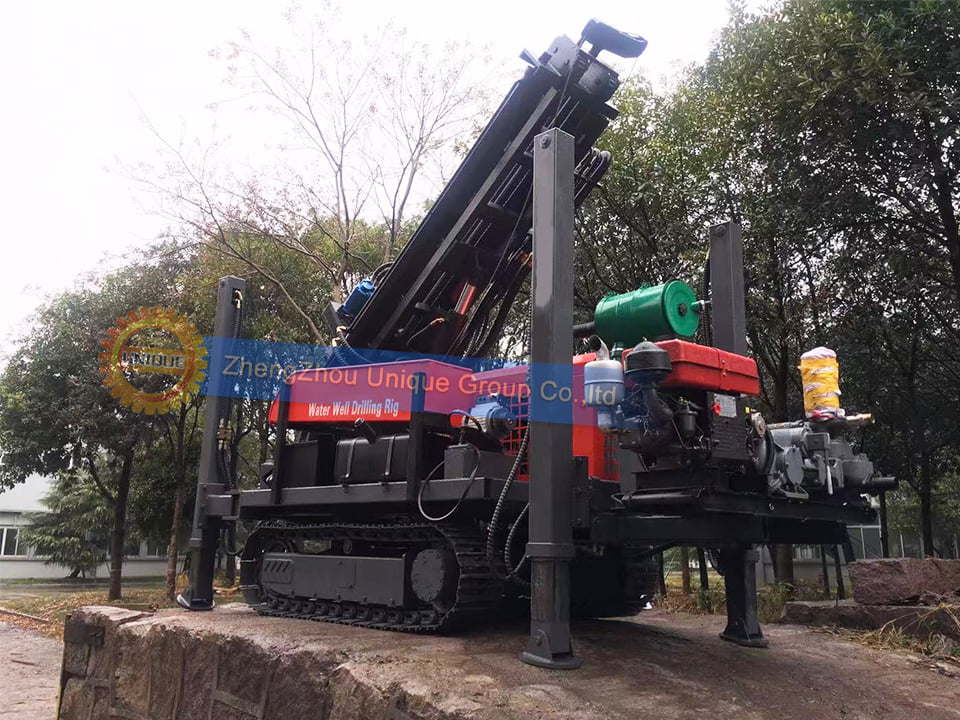
Drilling operations When drilling wells in different geological layers, each soil layer may bring specific challenges. The treatment method of each soil layer has unique operating skills and technical requirements. If you want to learn more, please contact us.