How to drill a water well?
Drilling a water well is a very complex project, and this article is a simple introduction to how to go about drilling a water well by giving you a brief overview of the equipment and processes needed to drill a water well.
I.What equipment do I need to drill a water well?
Drilling a water well is a systematic project that requires a variety of equipment to work together. The following is an overview of the main equipment and its uses:
1.Core drilling equipment
Types of drilling rigs: wheel-type water well drilling rigs , crawler water well drilling rigs and truck-mounted water well drilling rigs.
Function: Provide power to drive the drill bit to break up the formation and complete the drilling.
Drill pipe and drill bit
Drill pipe: Hollow steel pipe, connecting the drilling rig and drill bit, transmitting power and circulating medium.
Drill bit: choose the type according to the geology (e.g. three-cone bit, PDC bit, diamond bit, etc.).
Mud circulation system
Mud pump: pumps mud (water + clay/polymer) into the well to cool the bit and carry rock chips.
Vibrating screen/cyclone: separates rock chips from mud, purifies and reuses them.
Mud pool: store and mix mud.
2.Wellbore Construction Equipment
Casing and Well Tubing
Surface casing: protects the shallow well wall from caving.
Production casing: installed above the aquifer to prevent contamination.
Filter pipe: well pipe with pores or screens, placed at the aquifer location to filter sand particles.
Cementing Equipment
Cement pump: injects cement slurry between the casing and well wall to fix the casing and seal the formation.
3.Pumping and Testing Equipment
Pumping equipment
Submersible pumps: for deep well pumping (head can reach hundreds of metres). Deep well pumps: for high flow requirements.
Testing equipment
Flow meters: to measure water output.
Water level meter: monitors changes in groundwater level.
Water quality analyser: to detect the pH value, mineral content, pollutants, etc. of the water.
4.Auxiliary Equipment
Power and transport equipment
Diesel generator: Provide power for remote areas.
Crane/Crane: Install casing and pump body.
Transport vehicles: to carry large equipment such as drilling rigs and casing.
Safety equipment
Protective gear: helmets, goggles, non-slip boots, etc.
Wellhead cover/warning signs: to prevent people or foreign objects from falling in.
5.Special geological equipment
Air compressor: for air drilling (arid areas or formations prone to collapse).
Core sampler: to obtain stratigraphic samples for analysing geological structures.
Directional drilling tool: to adjust the drilling trajectory (avoiding obstacles or directional water extraction).
Points to note
Geological exploration first: use electro-methodometer or geological radar to determine the location and depth of aquifers.
Environmental requirements: Properly dispose of waste mud to avoid contamination of soil and groundwater.
Professional team operation: Drilling involves high-pressure, mechanical work, which needs to be performed by experienced personnel.
Post-maintenance: Regular cleaning of well walls and replacement of screens to extend the life of water wells.
By choosing a reasonable combination of equipment, it can be adapted to different geological conditions to ensure that the water well is built efficiently and safely.
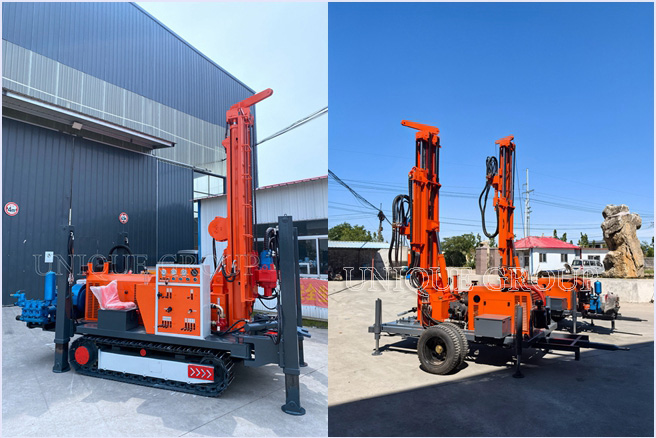
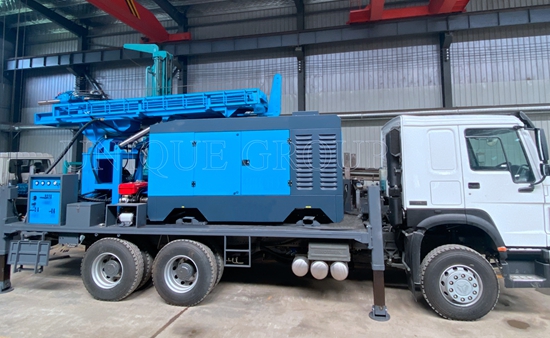
II.What is the process of drilling?
1.Preliminary Preparation
Geological exploration and site selection
Hydrogeological survey: analyse the distribution of underground aquifers (e.g. sand layer, fissure rock layer) through geological maps, satellite images or field surveys.
Electro-mechanical exploration/geological radar: to detect the depth and storage capacity of underground water and avoid pollution sources (e.g. septic tanks, rubbish dumps).
Determine the well location: choose a location with higher terrain and convenient drainage, away from pollution sources.
Equipment and material preparation
Drilling rig selection: choose rotary drilling, percussion drilling or air drilling according to the hardness of the formation (soft soil, hard rock).
Preparation of consumables: drill bit, casing (PVC/steel pipe), water filtering pipe, cement, bentonite (raw material for mud).
Safety measures: set up a warning area, check the stability of equipment (anti-tipping), and prepare a first aid kit.
2. Drilling construction process
1)Hole opening and surface casing installation
Open the hole with short drill pipe and larger drill bit.
Drill to a stable stratum and lower the surface casing .
The outer ring of the casing is filled with cement slurry to seal it and isolate it from surface contamination.
2)Drilling of the main well section
Circulation medium selection:
Mud drilling: clay + water (suitable for loose stratum, stabilising the well wall).
Air drilling: compressed air (hard rock formation, reduce water consumption).
Drilling process:Connect the drill pipe section by section, the drill bit continuously breaks up the formation, and the mud pump circulates and discharges the rock chips.
Samples are taken and analysed every 3-5 metres of drilling to confirm stratigraphic changes and aquifer locations.
Cope with complex strata:
Sand layer: increase mud viscosity to prevent hole collapse.
Pebble layer: change to percussion drill bit or alloy drill bit.
Fissured rock layer: control drilling pressure to avoid jamming.
3)Lowering production casing and water filtering pipe
Locate the aquifer: Determine the depth of the aquifer through rock chips and logging data.
Install water filter pipe: Install water filter pipe with screen/wrap mesh (e.g., bridge-type water filter pipe) in the water-bearing section, and fill the outside with gravel (to increase water permeability).
Seal the non-target layer: seal the upper and lower sections of the filter pipe with water stop rings or cement to prevent sewage from mixing.
4)Well washing and pumping test
High-pressure well washing: Repeatedly flush the well wall with water or air compressor to remove mud and fine particles.
Pumping test:Install a submersible pump to pump water continuously for 24-48 hours and record the water output and water level drop depth.
Calculate the sustainable extraction capacity of the well by means of a formula (e.g. using the Tess formula).
Water quality test: Take samples and send them to the laboratory to analyse microorganisms, heavy metals and other indicators.
5)Regular Maintenance
Clean the silt and sand at the bottom of the well every 1-2 years, and acid wash to remove carbonate scaling.
Check whether the screen is clogged and replace the broken parts in time.
Scenarios applicable to different drilling methods
Drilling methods Applicable formations Advantages Limitations
Rotary drilling Clay, sand, medium-hard rock High efficiency, can work in deep holes Hard rock requires frequent change of drill bits
Percussive drilling Pebble layers, hard rock High penetration, low cost Slow progress, high noise level
Air drilling Arid zones, fissured formations Water saving, fast debris removal Dependent on air compressor, dust pollution.
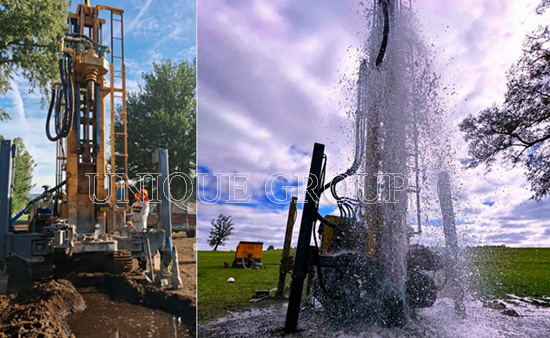
How to clean and maintain drilling equipment after work?
Cleaning and maintenance of drilling equipment is a key step to ensure the life of the equipment and the safety of subsequent operations. The following are the detailed procedures and precautions for cleaning and maintenance of equipment after drilling is completed:
I.Equipment cleaning process
1)Drilling Rig and drill pipe cleaning
Remove mud residue :Use high-pressure water gun to flush the inner and outer walls of the drill pipe, the power head of the drilling rig and the gripper, focusing on cleaning the mud and clumps of rock chips.
Stubborn stains can be brushed with alkaline cleaning agent (e.g. sodium hydroxide solution) after soaking.
Rust prevention treatment:Dry the surface after cleaning, spray antirust oil (such as WD-40) or apply grease .
When stored for a long time, the drill pipe should be hung vertically or placed flat on a dry stand to avoid deformation.
2)Mud circulation system cleaning
Mud pump and pipeline :Flush the pump body, valve and pipeline with clean water circulation until clear water is discharged.
Check the pump body seals for wear and replace the aged parts.
Vibrating screen and cyclone :Disassemble the screen, remove blocked fine particles with a soft brush, check for screen breakage .
Flush the inside of the cyclone cone with high-pressure water to prevent sediment slating.
Mud pool cleaning:Waste mud needs to be disposed of according to environmental protection requirements , and residues at the bottom of the pool are thoroughly removed.
3)Maintenance of drill bit and auxiliary tools
Drill Bit Cleaning: Soak the drill bit in diesel oil or special cleaning solution to remove the adhering rock chips and grease.
Core tube/sampler: Clean the inner wall of rock dust after disassembly and apply silicone grease to prevent rusting.
II.Key Equipment Inspection and Maintenance1)Power system maintenance
Diesel engine ,Change oil, filter and air filter, check coolant level and any leakage.
Clean dust and oil on the radiator surface to ensure cooling efficiency.
Hydraulic System,Check the cleanliness of the hydraulic oil (if turbid, replace it), and troubleshoot leakage of oil pipe joints.
Clean the breathing valve of hydraulic oil tank to prevent impurities from entering.
2)Electrical system maintenanceDisconnect the power supply and blow out the dust in the control cabinet with compressed air.
Check whether the cable insulation is broken and whether the joints are oxidised (apply conductive paste to prevent corrosion).
Test whether the emergency stop button and overload protection device are normal.
3)Treatment of wellhead equipment
Disassemble and clean casing wire guards and wellhead flanges, and apply grease to prevent rust.
Check the wear and tear of the tooth plate of the hanger card and kava, and replace them if the wear and tear exceeds 30%.
Through standardised cleaning and maintenance, the equipment failure rate can be reduced, the service life can be extended (usually upgraded by 30%-50%), and the safety risk of subsequent drilling operations can be reduced.
If you need to drilling a water well or related machinery, welcome to contact us, we will send you a professional suggest and scheme.
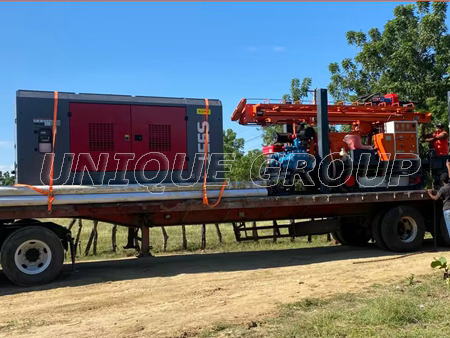
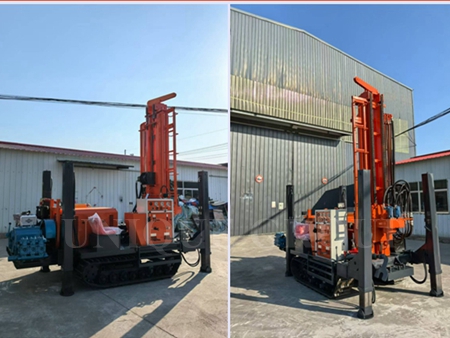