What are some tips for operating a hydraulic water well drilling rig?
What are some tips for operating a hydraulic water well drilling rig?
As an efficient and professional drilling equipment, hydraulic water well drilling rig plays a vital role in obtaining groundwater resources, conducting geological exploration and geothermal development. Understanding its correct operation process, common faults and solutions is of great significance to ensure the smooth progress of drilling work, improve work efficiency, extend the service life of equipment and ensure operation safety.
I.What is the right workflow of a hydraulic water well drilling rig?
A hydraulic water well drilling rig is a mechanical device that is powered by a hydraulic system and is specifically used for purposes such as drilling water wells, geological exploration, and geothermal development. Its workflow can be divided into several key steps, each of which has specific operations and functions:
1.Preparation
Before starting drilling, it is essential to prepare the equipment. It mainly includes the following aspects:
Equipment inspection: Check whether the various components of the drilling rig are intact, whether the hydraulic system is normal, and whether the electrical equipment is connected stably.
Installation and positioning: Position the drilling rig according to the drilling site. Use a level to ensure that the drilling rig is erected in a horizontal position and confirm that the drilling rig can effectively complete the scheduled work.
Debugging and testing: Debug the hydraulic system before drilling to ensure that the hydraulic pump, hydraulic motor, etc. are working properly and that the drill bit and drill pipe are well connected.
2.Hydraulic drive system operation
The hydraulic water well drilling rig is powered by a hydraulic system, and the core power during the working process comes from the hydraulic system.
Hydraulic pump start: After the hydraulic pump is started, the hydraulic oil is pressurized and transmitted to each hydraulic component through the pipeline to form the required working pressure.
Hydraulic motor and hydraulic cylinder: The hydraulic motor is used to drive the drill bit to rotate, and the hydraulic cylinder provides lifting power to adjust the depth of the drilling tool.
3.Drill bit rotation and footage
Drill bit rotation: The hydraulic motor drives the drill bit to rotate, and the rotation speed of the drill bit can be adjusted according to the different needs of drilling. The drill bit usually uses an alloy material with higher hardness, which can break the underground rock formation.
Footage: The drilling rig controls the up and down movement of the drill string through the hydraulic system to push the drill bit underground. The footage speed of the drilling rig is usually slow, but stable, ensuring that the underground water source can be gradually opened.
4.Circulation flushing and slag removal
Circulation flushing: During the drilling process, in order to cool the drill bit and take away the cuttings, a circulating flushing fluid (such as mud or clean water) is usually used. The flushing fluid flows into the well through the drilling pipeline, flushing the drill bit and the well wall, and taking the cuttings out of the wellhead.
Slag discharge system: After the flushing fluid passes through the wellhead, the cuttings and other impurities are discharged from the wellhead through the slag discharge system to keep the well wall stable and avoid hole collapse.
5.Adjustment and control
Depth control: The hydraulic system accurately controls the depth of the drill bit to prevent the drill bit from going too deep or drilling improperly.
Pressure monitoring: The pressure of the hydraulic system and the formation pressure during drilling are monitored by a pressure gauge to ensure that the drilling rig works within a reasonable pressure range to avoid the drill bit getting stuck or equipment damage.
6.Well support and hole formation
Support pipe installation: When drilling to a certain depth, the well wall may be unstable. At this time, it is necessary to install a well wall support pipe (such as a steel pipe or a cement pipe) to prevent the well wall from collapsing.
Hole formation: As drilling proceeds, the drilling operation gradually completes the formation of the hole wall and provides a stable aperture for subsequent water well construction.
7.End of drilling and disassembly
Drilling completion: When drilling to the required depth, the drilling rig stops drilling and completes the well construction task.
Disassembly and cleaning: gradually disassemble the drilling equipment, clean the drilling tools, hydraulic system, etc., and prepare for the next operation.
8.Data recording and reporting
During the drilling process, the drilling rig is usually equipped with a data acquisition system to record the drilling depth, formation characteristics, hydraulic system pressure and other data. These data are of great reference value for subsequent water well development and geological exploration.
The workflow of the hydraulic water well drilling rig gradually completes the water well drilling operation through a series of hydraulic power systems, drill bit rotation, footage control, flushing and slag removal. Through precise hydraulic control and reasonable operation procedures, the efficiency and safety of drilling are ensured. If the hydraulic water well drilling rig is not operated properly, what failures occur? And how to solve and prevent the failure? Follow us to learn more information, thanks.
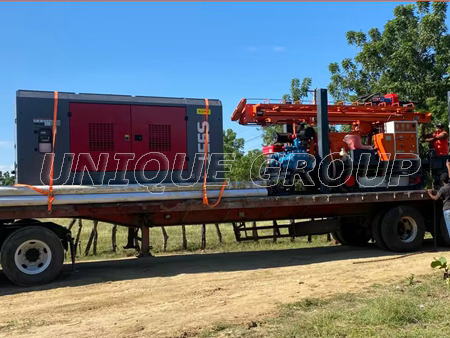
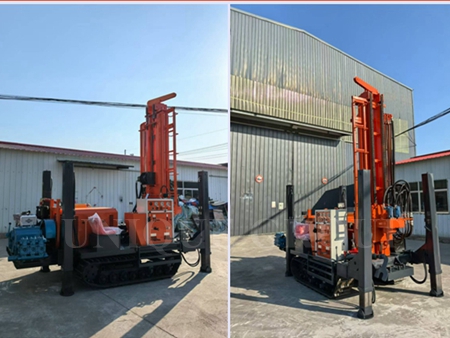
II.How to solve and prevent the failure?
The common troubleshooting and prevention methods for hydraulic water well drilling rigs are as follows:
1.Hydraulic System Failures
(1)Insufficient / unstable pressure
Manifestation: During the working process of the drilling rig, the speed slows down obviously, the power output is insufficient, and it is impossible to carry out drilling and other operations normally. For example, the rotational speed of the drill bit decreases, and the drill pipe is weak in lifting or lowering.
Reason: there may be blockages in the oil circuit, such as impurities, dirt, etc., which impede the normal flow of hydraulic oil; leakage of oil pipes, joints and other parts, resulting in the loss of hydraulic oil, and the system pressure can not be established; wear and tear of the internal parts of the hydraulic pump, damage, so that it can not be properly pressurized; pressure relief valve failure, which may be premature pressure relief or inaccurate pressure relief; insufficient hydraulic oil, or contamination of the oil, which affects the fluidity and pressure transfer performance. fluidity and pressure transfer performance.
Solution: Conduct a comprehensive inspection of the oil circuit, use special tools to clean up the blockages in the filters and tubes, and if necessary, replace the damaged or badly blocked parts. Check the oil level of the hydraulic oil, insufficient to timely supplement the hydraulic oil that meets the requirements of the equipment. If the oil is contaminated, the oil should be completely replaced with new oil to ensure that the oil is clean. For the pressure relief valve, the pressure can be adjusted according to the equipment manual, if it can not be repaired, then replace the new pressure relief valve. If it is determined that the hydraulic pump is damaged, it is necessary to disassemble the hydraulic pump, check the internal parts, such as gears, plungers, etc., and replace the damaged parts or directly replace the new hydraulic pump.
(2).Oil temperature is too high
Reason: the drilling rig has been in no-load operation for a long time, the hydraulic oil is circulating in the system, but there is no actual work done, resulting in the conversion of energy into heat, so that the temperature of the oil rises. Failure of the cooling system, such as cooling fan does not turn, radiator blocked, etc., can not effectively dissipate heat. The viscosity of the hydraulic oil used is too high, increasing the flow resistance of the oil in the pipeline and components, thus generating too much heat.
Preventive measures: In actual operation, try to avoid running the drilling rig with no load, and turn off the hydraulic system in time during non-operating hours. Regularly maintain the cooling system, clean the dust and debris on the surface of the radiator, and check the motor and transmission parts of the cooling fan to ensure its normal operation. According to the environment and seasonal changes in the use of equipment, select the appropriate viscosity of the hydraulic oil, and in high temperature environments, use hydraulic oil with a slightly lower viscosity to reduce the resistance of the fluid flow.
2.Mechanical component failure
(1)Stuck drill (clamping drill)
Types and treatment: When encountering stone or rock slag pinch drilling, try to string the drilling tool up and down, use the impact force of the drilling tool to loosen the pinch drilling material, and at the same time increase the flow rate and pressure of the flushing fluid to flush the rock chips and stones out of the wellhead. If the drill jam is caused by a broken bit or a key slipping out, do not forcefully rotate the drilling tool to avoid more serious damage. You should try to remove the broken bit or slipped key by reversing the rotation of the drilling tool, or lift the drilling tool while rotating it slowly to gradually remove the jammed drilling tool.
Prevention: Before each drilling operation, carefully check the wear of the drill bit, and replace the badly worn bit in time. During the drilling process, adjust the drilling parameters according to the ground conditions and avoid overloaded drilling to prevent excessive wear or damage to the drill bit.
(2)Damage to drill pipe/bit
Performance: The drilling efficiency is obviously reduced, and it takes more time and power to drill the formation that could be drilled smoothly. At the same time, abnormal noises such as banging and friction may be heard during drilling.
Solution: For drilling bits with serious wear, you can choose to replace them with better wear-resistant ones, such as those with diamond composite inserts, in order to improve the service life and drilling efficiency of the drill bits. Regularly check the connection of the drill pipe to make sure it is firmly connected, and tighten it in time if it is loosened, meanwhile check whether the drill pipe is bent, cracked, etc., and replace it in time if it is damaged.
(3).Winch brake slipping
Reason: The surface of the brake belt is contaminated with oil, which reduces the friction between the brake belt and the brake wheel; or the gap of the brake is adjusted too large, resulting in the inability to effectively hold the brake wheel when braking.
Treatment: Use cleaner to thoroughly clean the oil on the surface of the brake band to ensure that the surface of the brake band is dry and clean. Then, according to the equipment manual, use special tools to adjust the gap of the brake, so that it returns to the appropriate range to ensure the braking effect.
3.Electrical and Power System Failures
(1)Low battery voltage
Solution: Check whether the charger is working properly and whether the connection line between the charger and the battery is loose or broken. If the charger fails, repair or replace the charger in time. At the same time, check the electrolyte level of the battery, add distilled water or special electrolyte when insufficient. If the battery has been used for a long time, aging seriously, can not store enough power, it is necessary to replace the battery with a new one.
(2)Generator output is not stable
Cause: The rotor of the generator may be loose, resulting in the inability to cut the magnetic lines of force stably during operation, thus making the output voltage unstable. In addition, poor contact of the circuit connection parts, such as loose terminals, aging and broken wires, etc., will also affect the normal transmission of current, resulting in unstable output.
Treatment: open the generator shell, check the fixing of the rotor, and use tools to tighten the loose rotor. At the same time, conduct a comprehensive inspection of the circuit connection parts, reconnect the loose terminals, replace the aging and broken wires, and ensure that the circuit is connected reliably to ensure that the generator outputs a stable voltage.
4.Operation-related faults
(1)Slag discharge is not smooth
Cause: The slurry pump may be faulty, such as worn pump body, damaged impeller, etc., resulting in the inability to provide sufficient pressure and flow rate to transport flushing liquid and carry rock chips. The slag discharge pipeline may be clogged, such as accumulation of rock chips, entry of foreign objects, etc., preventing the discharge of flushing fluid and rock chips. Insufficient circulating fluid to create effective flushing and slag discharge power.
Solution: Dismantle and inspect the mud pump, replace the worn pump body, impeller and other parts to ensure that the mud pump can work normally. Use high-pressure water gun or special pipeline dredging tools to clean up the slag discharge pipeline, remove the blockage, and ensure that the pipeline is unobstructed. Check the level of circulating fluid and replenish the circulating fluid in time to ensure that the circulating fluid is sufficient to meet the demand of slag discharge.
(2)Well Wall Collapse / Drill Shift
Prevention: In the process of drilling, strictly control the drilling speed to avoid excessive impact on the wall. Keep the mud performance stable, and adjust the density, viscosity and water loss rate of the mud according to the formation conditions, so as to enhance the support and protection of the mud to the well wall. For complicated formations, such as quicksand layer and fault, advance reinforcement measures can be taken before drilling, such as injecting chemical curing agent and installing over-head support to improve the stability of the well wall and prevent collapse and drilling offset.
Hydraulic water well drilling rig plays an important role in modern engineering construction, and its operation process covers all aspects from the preparation work to the end of drilling, and each link is closely connected, which has a direct impact on the quality and efficiency of drilling. In the process of using the equipment, due to the complexity of the equipment and the diversity of the operating environment, a variety of failures may occur, including the hydraulic system, mechanical components, electrical and power systems and operation-related failures. Through in-depth understanding of the performance, causes and solutions of these failures, and taking effective maintenance and preventive measures, such as regular maintenance of equipment, standardized operating procedures, rapid response to failures, etc., you can significantly reduce the failure rate of the equipment, improve the reliability and service life of the equipment, to ensure that the hydraulic water well drilling rigs can be operated efficiently and safely, and provide a strong guarantee for various types of engineering construction.
If you are considering carrying out water well drilling, geological exploration or geothermal development projects, and need hydraulic water well drilling rigs with excellent performance, or have any questions about the operation and maintenance of the equipment, our professional team is always ready to serve you. We offer a wide range of high-quality hydraulic water well drilling rigs, each of which has been carefully designed and rigorously tested to ensure that it meets your different operational needs. Whether you are in need of equipment purchasing, technical consulting, or looking for customized solutions, please do not hesitate to contact us. Send us your inquiry to start your efficient and reliable drilling journey, and we will provide you with detailed and professional replies as quickly as possible to help your project move forward smoothly and create more value.