What is a screw air compressor commonly used in DTH blasting rigs?
Screw air compressor is one of the key supporting equipments in DTH drilling rigs, which is mainly used to provide high-pressure air to drive the impactor of the drilling rig to work and discharge the rock chips out of the drilling hole. The following is a detailed introduction about screw air compressor and its advantages:
I.What type of screw air compressor is used on DTH blast drilling rigs?
Screw air compressors in DTH drilling rigs are usually divided into the following two categories:
1.Fixed screw air compressor
Suitable for fixed operation places (such as mines, quarries), connected to the drilling rig through pipes or hoses.
The power range is wide, which can meet the demand of large diameter and deep hole drilling (e.g. 20-40 cubic metres/minute, pressure 10-35 bar).
2.Mobile screw air compressor
Integrated in the drilling rig or trailer, easy to use in the field or strong mobility conditions (such as construction sites, tunnel construction).
Usually equipped with diesel engine drive, adapted to the environment without power supply.
Electric vs. diesel options
Electric screw air compressor: high energy efficiency, low noise, suitable for stable power supply.
Diesel screw air compressor: strong power, adapted to remote areas or mobile operation needs.
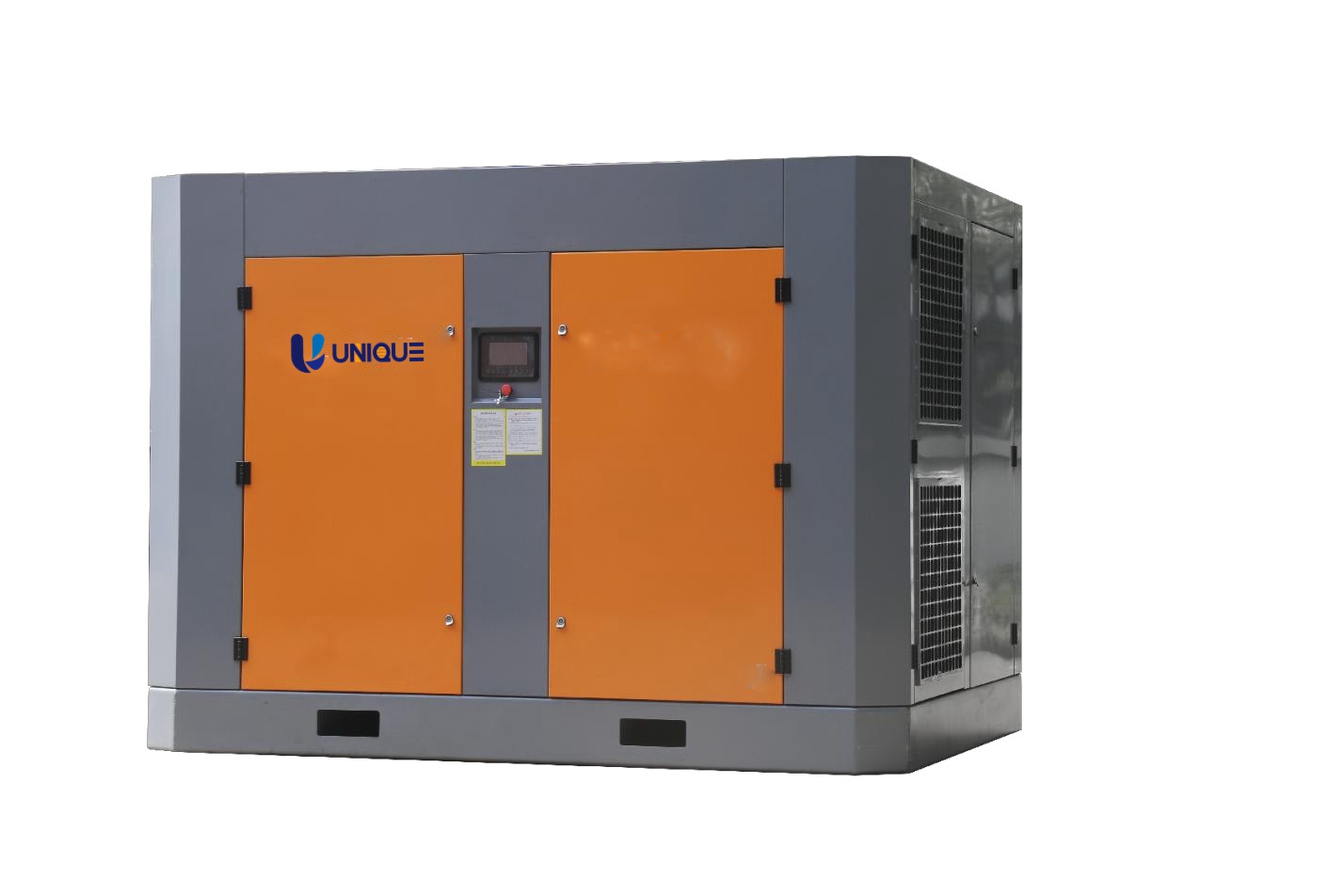
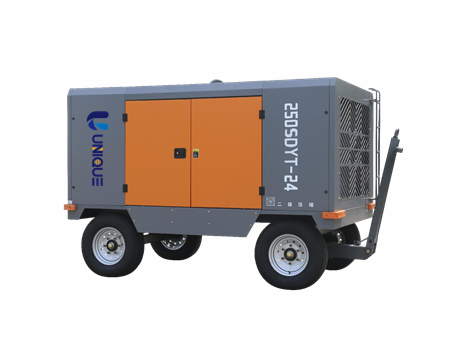
II.What are the advantages of screw compressors?
1.Efficient and stable air supply: the twin-screw rotor design has high compression efficiency, which can provide continuous and stable high-pressure air flow to ensure that the impactor of the DTH drilling rig works efficiently and reduce air pressure fluctuations in the drilling process.
2.Resistant to harsh working conditions: The screw compressor is highly adaptable to dusty and humid environments, and is equipped with multiple filtration systems (e.g. intake filter, oil filter), which is suitable for harsh working conditions such as mines and tunnels.
3.Energy-saving and environmental protection: Adopting variable frequency technology (VSD) to regulate the output, supplying air on demand and reducing energy consumption (about 30% energy saving compared with piston compressor). The diesel model meets the National III/National IV emission standards, reducing environmental pollution.
4.Low maintenance cost: simple structure, few moving parts, low failure rate, long maintenance cycle (usually every 2000-8000 hours maintenance). Modular design facilitates quick replacement of wearing parts (e.g. oil filter, air filter).
5.Long life and reliability
Core components (such as the host screw) using high-strength alloy steel, life expectancy of up to 40,000 hours or more, suitable for high-intensity continuous operation.
Intelligent control, modern screw compressor integrated PLC control system, real-time monitoring of pressure, temperature, oil level and other parameters, support for automatic start and stop, fault alarm, enhance operational safety.
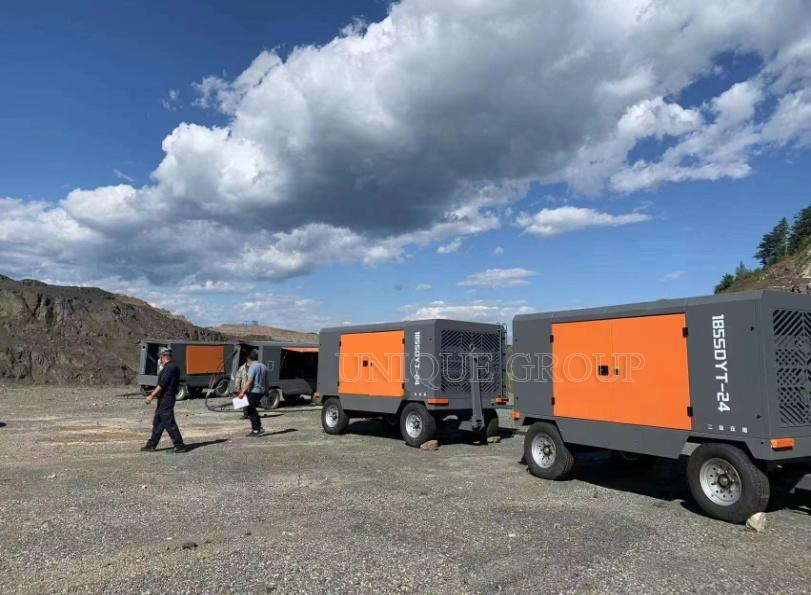
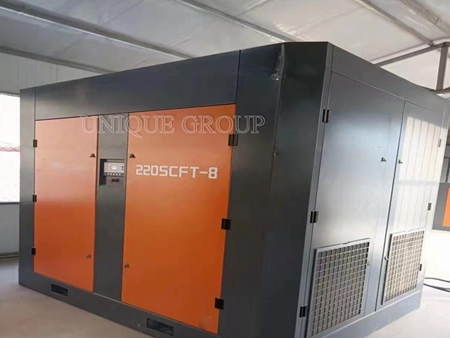
III.Advantages compared with other types of air compressors
Compared with the traditional piston type air compressor, the advantages of screw air compressor are especially obvious:
Lower noise: the screw runs smoothly and the noise is 10-15 decibels lower than piston type.
Less vibration: Reduced wear and tear on the rig structure, prolonging the life of the equipment.
Pure air supply: low oil content in export air (≤3ppm), avoiding contamination of drilling holes or clogging the impactor.
IV.What are the common failures of screw air compressor? How to solve the problem?
1.Insufficient air exhaust
(1) Possible causes: excessive air consumption
Elimination method: Check whether the air-using equipment and compressor exhaust volume are appropriate.
(2) Possible cause: High pressure air leakage
Elimination method: Check the air supply piping and valves for leaks.
(3) Possible cause: Air filter clogging.
Elimination method: Check whether the instrument shows a signal that maintenance is required, and replace the filter element if necessary.
(4) Possible causes: Oil-air separation filter element clogging
Remedy: Replace the oil separation filter element, oil filter element and oil.
(5) Possible causes: regulator out of adjustment or damaged
Remedy: Adjust the regulator, see Chapter 4 Operating Procedures. Check regulator diaphragm and replace if necessary.
(6) Possible causes: diesel engine speed is too low
Remedy: Adjust speed, or check diesel filter.
(7) Possible causes: insufficient intake valve opening
Treatment: check the control pipeline
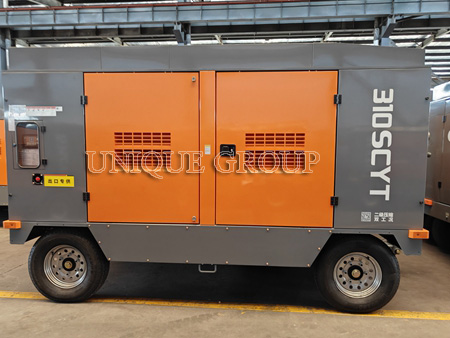
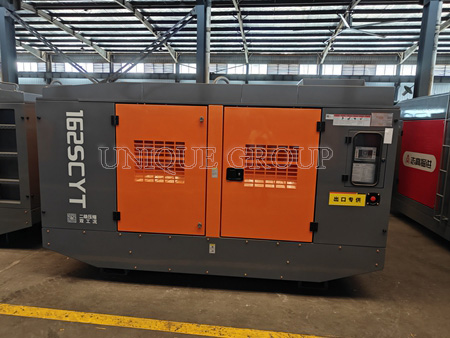
2.Insufficient air supply pressure
(1) Possible causes: excessive air demand.
Treatment: Check whether the air-using equipment and compressor exhaust volume are appropriate.
(2) Possible reasons: air filter clogging.
Treatment: Check whether the instrument shows a maintenance signal, and replace the filter element if necessary.
(3) Possible causes: high-pressure air leakage
Treatment: Check whether there is leakage in the air supply pipeline and valve.
(4) Possible causes: regulator out of adjustment or damaged
Treatment: Adjust or replace
(5) Possible cause: Oil-air separator oil level is too low.
Treatment: Add oil. Check for leakage.
(6) Possible cause: Oil cooler too dirty or clogged
Remedy: Clean oil cooler core fins.
(7) Possible cause: Loose or damaged fan belt
Remedy: Adjust the tensioner pulley, or replace the belt.
(8) Possible cause: Temperature control valve thermal element failure
Remedy: Replace the thermal element.
(9) Possible cause: Temperature control valve to the head oil pipe blockage
Remedy: Unclog the oil pipe.
(10) Possible cause: Plugged head main oil inlet fitting
Remedy: Unclog the connector.
With its high efficiency and stability, energy saving and environmental protection and low maintenance characteristics, the screw air compressor has become an ideal power source for DTH blasting rigs. When selecting one, it is necessary to match the right type and parameters to the working conditions (power supply, mobility, drilling depth/hole diameter) to maximise the rig’s operating efficiency and reduce the overall cost. Please feel free to contact us for further advice on selection or technical parameters!